What is the resolution of a gage?
A measuring device has the purpose to provide a value to a characteristic of an object, process or phenomenon. In order to provide that value, the gage has a display or scale where the assigned value is shown.
The smallest readable unit or mark on the scale of the gage is called resolution or, better said, the smallest unit of measure that a gage can provide along its measuring range is the device resolution.
In the AIAG MSA manual, the discrimination is described as the measurement resolution or smallest detectable unit of the measurement device. This is the scale limit and it is a inherent property of gage design, reported as a unit of measurement.
Can you identify the resolution by the digits shown on the display?
In some cases you may but in others you may not. It depends on the device. The resolution can be considered as the smallest increment of the value which can be measured. In gages with a digital display, the number of digits (0.000) may not really tell what the resolution is. The smallest readable increment could be every 0,005 units for instance.
Some experts consider the apparent and effective resolution. Apparent resolution is the smallest readable unit on the scale and effective resolution is the smallest increment in value based on the measurement system variation observed during a study and calculated using a reference confidence level (i.e. 95%).
Why is it so important?
When we measure, we obtain values and make decisions based on the results. Depending on the characteristic to be measured, its magnitude and purpose, the gage resolution should be adequate. The tolerances or limits set or defined to qualify the measurand and discriminate whether the value is ok or not ok are also important.
There are many factors of a measurement system that can affect the reliability of the measurements obtained. The resolution is very important and one of the first elements to be considering when choosing a measuring device.
Measurement uncertainty.
If you cannot rely on the information you get, you cannot have the certainty that you will make the right decision.
Imagine you are travelling to a very far destination and you have to take a big piece of luggage with you. The allowed maximum weight included in your flight class is 40 pounds. What can it happen if the scale you use to measure does not provide reliable information?
a. If the scale “measures” more than the bag really weights, you will take with you less than you are allowed to.
b. If the scale shows less than reality, you will have to pay extra fees at the airport.
Resolution and uncertainty.
Especially in cases where the measured values are very close to the limits (upper or lower), the resolution may play a very important role.
Let’s imagine that you are a quality inspector and have to control the quality of plastic cards. The size cannot exceed 9.5 cm. If you had only these three options as shown in the image below, which gage would you choose and why?
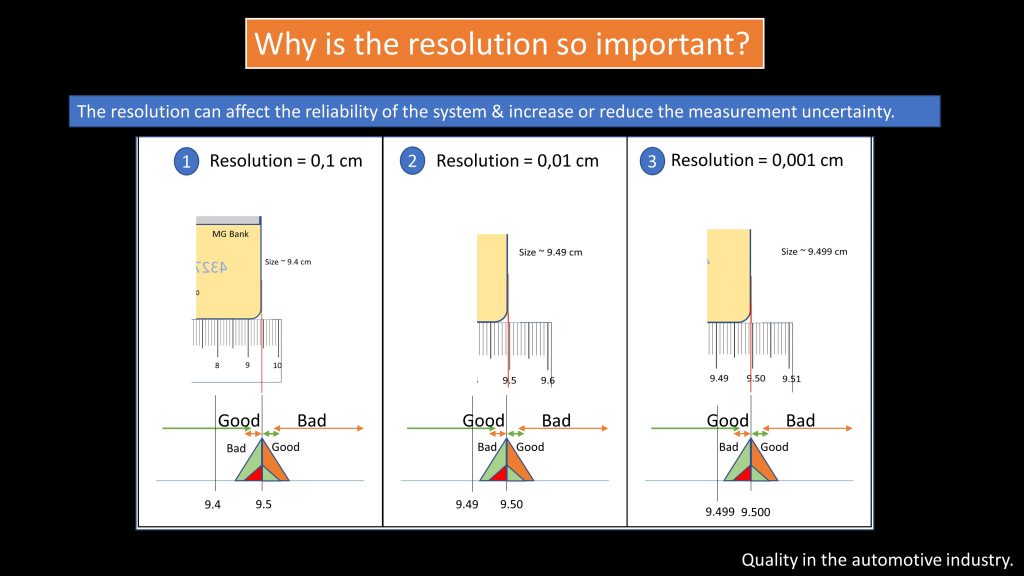
Did you choose the gage number 3? Resolution is not the only source of uncertainty. However, if we assume that the shape of the cards remains the same and the unseen sides of the card are aligned to the zero, etc., the gage number 3 provides more information and we can have more certainty that the value 9.5 will not be exceeded. With gages 1 o 2 is more difficult to tell because the reference line falls between two marks. Is it still ok?
The green-red triangles show the area with the risk of errors. In some cases the appraiser may say the product is ok even if the valued is exceeded or, he can say nok even if the cards are still good.
Resolution analysis.
The MSA has a technique called resolution analysis to assess the quality of the measuring systems. The easiest assessment is to consider the 10-to-1 rule. The discrimination should be a tenth of the tolerance.
I have seen some auditors asking about nominal values in drawings or technical data and assessing the gage resolution as the smallest unit called in the drawing divided by 10. For example, in a drawing there was a dimension shown as 25.55 mm and the auditor consider the smallest unit called 0.01 divided by 10 and requested a gage resolution of 0.001 mm.
That can be a reference but is not necessary to use that math. Remember that the resolution is required to have as much certainty as possible in the measurement but, in the tolerance range. In the example mentioned, the drawing showed 25,55 +/- 0,05 mm and therefore the tolerance range was 25,60 – 25,50 = 0,1. The suggested resolution should then be 0.1/10 = 0,01 mm.
As you can see, this difference between 0.01 mm and 0.001 mm can lead to two different gages and probably two different prices, availability, etc.
As a general rule, the AIAG standard suggests a gage resolution of 10% while the VDA suggests 5%. However you can consider 5% or 10%:
- of the smallest unit shown in the dimensions.
- of the tolerance range.
- of the process variation.
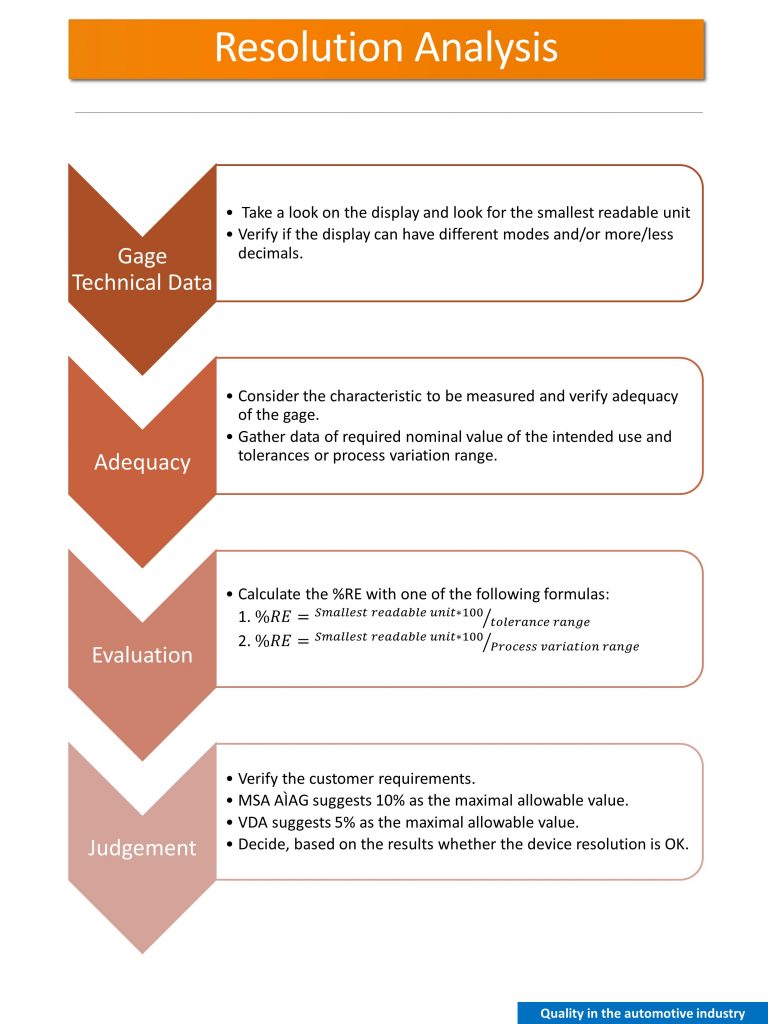
0 Comments