How reliable is a quality control by attributes?
And as you might have guessed, I cannot make a statement for all possible cases. However, I can recommend to use variables and measurements instead of relying on the perception of a person. This is not because persons are bad but, our judgement can be influenced by emotions, fatigue, pressure or stress, distraction, etc.
Even if this is known, in some cases, due to the nature of the product, its features, cosmetic requirements or cleanliness required, we need to rely on human perception and let workers evaluate with their senses.
If the attributes control is necessary, we should consider the following hints to get as good results as possible.
Suggestions to have good results
As mentioned before, there may not be any golden rule or magic formula which applies to all industries, process, products, etc. but, the following suggestions may be adapted to your needs and help you have good results.
- The control area needs to be adequate for the persons performing the control. Illumination, temperature, etc. should be such that the persons can focus to the task. Noise, vibration, interruptions and distractions should be avoided whenever possible.
- The evaluation criteria should be as clear and easy as possible. Boundary samples, a defect catalog or images with legends “OK” or “Nok” will make the decision a little bit easier.
- The ILO (international labor organization) suggest working conditions and rest periods for the appraisers. The more difficult the “recognition” is, the longer and more frequent the pause should be.
- Try whenever possible to implement a Go-No Go type of system. If the appraisers “only” need to decide between two conditions and the criteria is clear, the success rate will be higher. The more “quality levels” they have the worse result they will have.
- All operators should be trained regularly in order to keep a standard working method. Criteria, images, boundary samples and other support tools should be explained and the results evaluated during every training session. All appraisers should be able assess the characteristic in the same way and ideally, with the same results.
- Perform regularly a Gage R&R – Yes!!! and you will realize how well work the appraisers and the whole team.
GR&R by attributes
The GR&R by attributes is one of the techniques of the MSA measurement system analysis and exactly as any other of such techniques, it will help you assess how capable your system is to “catch” the bad parts and to identify and accept the good ones.
What kind of attributes can be considered for a GR&R?
Basically any that you have defined in your process. They can be like these:
- Aspect defects like scratches ( acceptable / not acceptable)
- smell and/or taste (intensity)
- color matching
- surface texture or appearance
- corrosion, bad finishing or discoloration
- cracking, haze
- presence or absence of features, defects, component, etc.
How to prepare the GR&R?
Depending on the manufacturing process, product and features to consider, you may have more than one workers who evaluate the parts. You can start by identifying which teams work together, how the defects are reported, statistics, pareto, etc.
The GR&R will show the degree of “accurate” identification of good or bad parts and how the appraisers agree or disagree on acceptance or rejection. As you may remember, a bad decision can lead to either one of the following errors:
- The part is ok but will be rejected and scrapped.
- The part is nok but will be released and delivered.
What do you need to perform the study?
- Similar to the preparation of a GR&R for variables, you (or the study coordinator) will need to select and rate 50 pieces and identify them (mark them) and make a professional assessment of good or bad for each part (recording which is which and marking in such a way that only the coordinator can tell which part is which). Please note that you will need to consider both. If all parts are good or bad, you will evaluate only one condition of the decision, either 100% good or 100% bad. As we have mentioned in other posts, the measurement system should be able to catch bad parts but also “accept” and “release” the good ones. Therefore, you need good and bad parts (50%-50%, 70%-30% but still both of them and mixed -randomly provided to the appraisers-).
- Three appraisers.
- Three trials (one trial is the complete assessment of 50 parts by one appraiser) for each appraiser.
- Data collection and organization.
Interpreting the results
As mentioned above, the results are better when the decision is only “accept and reject”. If a rating in more than two categories is required, the GR&R needs to be made in a slightly different way. Since I am convinced that simplicity is beautiful, I will consider further in this post only the go-no-go type of decision.
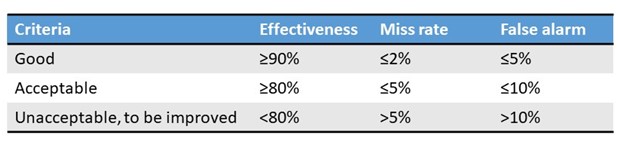
Effectiveness shows the degree of each appraiser and the team to judge the parts “bad or good” exactly as expected. Miss rate is the degree of misjudgement when saying the “part is ok” when the part is really bad. False alarm is the opposite, the judgement made is: “the part is not ok” while it was indeed ok.
The effectiveness should be 90% or higher with less than 2% miss-rate. Miss rate is considered worse than false alarm because the customer will receive bad parts while the false alarm will generate unnecessary scrap (but still, the customer will be protected).
The system will be evaluated with the “agreement” or “disagreement” for every part. Agreement is when all appraiser agree on the judgement as good or bad. The agreement will be counted as “effective” when the bad part is caught, otherwise as miss-rate or false alarm. The effectiveness of the whole team is important because will add-up all the individual decisions. The collective result is more important than the individual even though, both are critical to identify the problems to solve… either in clarity of criteria, boundary samples or the ability of the appraisers to judge the parts.
An image tells more than 1000 words....
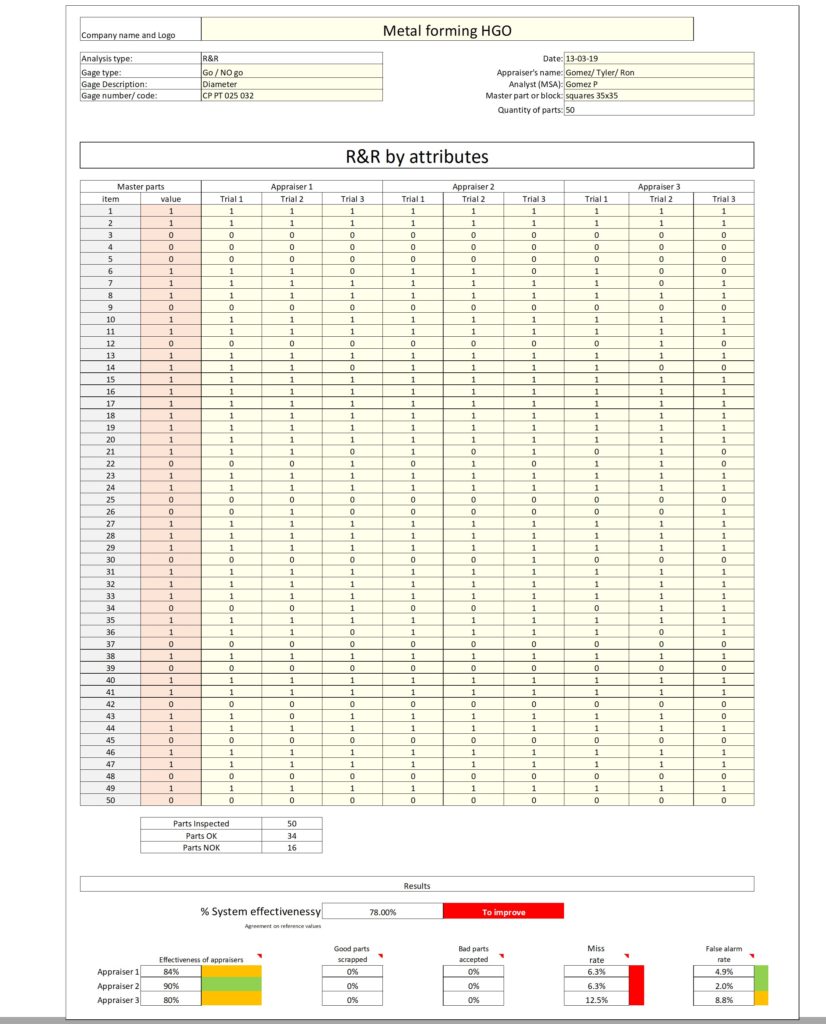
Do you need a free excel sheet?
You can directly go to the MSA section/calculation sheets and select the one you need or, go directly to the GR&R by attributes with this link.
I wish you a lot of success!!!!!
0 Comments